Композитные материалы в конструкции грузовых вагонов
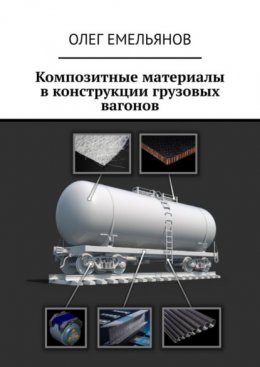
© Олег Емельянов, 2024
ISBN 978-5-0062-2111-6
Создано в интеллектуальной издательской системе Ridero
Раздел 1.
Введение в мир композитных материалов
1.1. Определение и общие сведения о композитных материалах
Композитные материалы – это искусственно созданные человеком материалы, которые получают соединением двух и более компонентов. Компоненты в существенной степени отличаются друг от друга по своим физико-химическим свойствам. Сочетание таких разнородных материалов приводит к тому, что образуются новые материалы с уникальными свойствами, отличными от исходного сырья. Комбинируя объемное содержание компонентов, можно получать композиционные материалы с требуемыми значениями прочности, жаропрочности, модуля упругости, абразивной стойкости, а также создавать композиции с необходимыми магнитными, диэлектрическими, радиопоглощающими и другими специальными свойствами.
Важно различать понятия композитный материал и композиционный материал. Они не всегда взаимозаменяемы.
Композитные материалы (композиты) состоят из матрицы и набивки. Матрица – это компонент, который непрерывный во всем объеме композиционного материала, связующее вещество. Набивка или арматура – компонент прерывистый, разделенный в объеме композиционного материала.
Композиционные материалы – материалы, состоящие из композиции (набора, совокупности) нескольких материалов, это более широкое понятие, в отличие от композита. Несколько компонентов при объединении дают новые свойства. При этом ярко выраженной границы раздела между компонентами на физическом уровне нет. Например, металлический сплав – это композиционный материал, т.к. для его получения происходит объединение нескольких компонентов. Главное отличие от композитов в том, что композиционный материал – однородный, он обладает одинаковыми свойствами в любой своей точке.
Принцип разработки таких материалов также отличается. Если композиты изначально разрабатываются, исходя из того, что каждый отдельный элемент конструкции возьмет на себя конкретные функции, то композиционный материал обладает едиными свойствами в любой своей точке, не зависящими ни от направления, ни от типа прикладываемой нагрузки.
1.2. История развития композитных материалов
Сегодня словосочетание «композитный материал» вызывает ассоциации с самыми прорывными технологиями и решениями, на которых уже строится будущее. Это не совсем верно: ведь самой идее композита уже несколько тысяч лет. Но, несмотря на весь прогресс, основной принцип создания композитов сохраняет свою актуальность и по сей день.
К числу первопроходцев по части получения и применения композитных материалов относят жителей Месопотамии – они населяли регион 3,5 тыс. лет до нашей эры. Именно там зародилась история композита, а именно материала, до сих пор используемого людьми, – фанеры. Было достаточно сложить несколько листов дерева друг на друга под разным углом, закрепить их примитивным клеем, и материал, доказавший свою эффективность на долгие сотни лет вперед, готов.
Сочетание клея и листов дерева образовало новый, куда более прочный и износостойкий материал, дошедший до наших дней. Это базовый принцип композита: объединение свойств уже существующих материалов. С того момента, как человек освоил этот принцип, технический прогресс начал ускоряться – композиты стали спутниками целых цивилизаций.
Папирус – композит. При его изготовлении спрессовываются слои горизонтальных волокон растения с вертикальными. В результате легкий, прочный, долговечный материал. Достаточно сравнить его с теми же месопотамскими глиняными табличками: громоздкие и неудобные, они по всем параметрам проигрывали изящному изобретению египтян. Папирус было удобнее хранить, и, по сравнению с «царапанием» по глине, на нем гораздо проще писать и рисовать.
Бетон – также композитный материал. Бетон впервые был описан римским архитектором Витрувием еще 2 тыс. лет назад. Ученый делал ставку на сочетание вулканического пепла и известняка, чтобы придать своим постройкам надежность и прочность. Использование нового материала позволило в значительной степени улучшить физико-механические характеристики сооружений. Бетон применялся практически везде, будь то храмы, многоэтажные дома, стадионы, гавани, мосты, акведуки или дороги. Где-то он даже вытеснил кирпич. Римский Колизей – одна из вершин античного зодчества – сохранился до наших дней благодаря тому, что в его строительстве применялся бетон. Секрет прочности римских конструкций во многом продиктован именно использованием бетона: этот пластичный материал выдерживал несколько десятков лет воздействия воды и при этом становился только прочнее.
Во все времена исследователи отмечали особую роль луков в военном могуществе кочевников, державших в страхе государства Европы и Азии в период XIII—XV веков. И это неудивительно – ведь луки, которые использовали завоеватели, были композитными. Такой лук состоял из дерева, костей и клея животного происхождения. Это легкое и простое для использования конниками оружие обладало рядом преимуществ даже по сравнению со знаменитыми английскими длинными луками: в отличие от последнего, монгольский композитный лук придавал стреле ускорение на протяжении всего «выстрела». Сама конструкция композитного лука и его гибкость придавали дополнительное ускорение стреле, что упрощало работу лучника и сказывалось на точности стрельбы. Оружие обеспечило преимущество на поле боя и заложило основу могущества Монгольской империи.
Настоящий расцвет использования композитных материалов пришелся на XIX—XX вв, когда плоды научно-технического прогресса изменили понимание человека о природе вещей.
В начале XIX века в строительстве вновь начал применяться бетон. Он вернулся в цивилизацию благодаря тому, что в 1796 году англичанин Д. Паркер запатентовал технологию получения романцемента – вяжущего материала, способного к затвердеванию и на открытом воздухе, и в воде. Смешанный с гравием, песком и водой цемент образовывал бетон. Этот строительный материал, отличавшийся своей пластичностью, завоевал новую популярность – впервые со времен Древнего Рима. Прочный и водостойкий материал плохо выдерживал нагрузку на растяжение, поэтому в качестве основного материала для несущих конструкций применялось железо в виде кованых стержней и полос. Но оно, в свою очередь, было подвержено коррозии, из-за чего перед человечеством стояла задача: найти более универсальный материал, способный сочетать свойства как бетона, так железа. Так придумали объединить два материала: арматура легко обволакивалась бетоном, тем самым оказываясь включенной в его массу. Сила сцепления железа с бетоном была огромной: материалы начинали работать как одно целое. Так появился железобетон – композит, ставший новой вехой в истории строительства. «Спрятанное» в бетон железо не ржавело и сохраняло свою прочность, а сам железобетон показал высокую огнестойкость. Материал показал себя как долговечный, устойчивый к воздействию температур и удобный в использовании – с железобетоном конструкции можно придать практически любую форму.
В середине ХХ в. композиты активно начали применяться в авиации: индустрия отчаянно нуждалась в новых материалах, и именно композиты позволили дать ответ на насущные вопросы инженеров.
Одной из основных разработок была дельта-древесина. Инженеры пропитывали слои шпона фенол- или крезолформальдегидной смолой, спрессовывали их и получали уникальный материал, который легче и прочнее многих сплавов на основе алюминия. Новый материал также был огнестойким и не покрывался плесенью. Дельта-древесина использовалась, например, в самолетах ЛаГГ-3, эксплуатация которых началась в 1941 году.
Также во время войны стало известно о радиопроницаемости композитов из стекловолокна. Эта, казалось бы, мелочь, смогла избавить пилота от риска остаться без связи: «обтекатели» из стекловолокна защищали радиомодули от внешних факторов, не мешая коммуникациям.
В 1960-х был изобретен углепластик: материал, состоящий из тонких нитей диаметром от 5 до 10 мкм. Он характеризовал себя как прочный, легкий, эффективно справляющийся с температурами и химической инертностью.
Сегодня композитные материалы являются полноценной индустрией, на которой основаны самые критические производства и сферы жизни. Список сфер, где применяются композиты, обширен: это не только авиация и космос, но и архитектура, автомобильная отрасль, энергетика, инфраструктура, судостроение, медицина, спортивная и рекреационная индустрии. Общий объем рынка композитов оценивался в $74 млрд в 2020 году, и, по, прогнозам, достигнет отметки в $112 млрд уже в 2025 году.
1.3. Типы и классификация композитных материалов
Композитные материалы состоят из двух основных компонентов: матрицы и армирующего материала (набивки). Матрица – это основной связующий материал, который держит вместе элементы набивки, обеспечивая форму конструктивного элемента в целом и ряд его основных механических свойств. Армирующий материал, зачастую волокна или частицы, обеспечивает требуемые механические свойства, такие как прочность и жесткость.
Классификация композитных материалов:
1. По материалу матрицы:
1.1. С металлической матрицей. Металлическая матрица упрочняется высокопрочными волокнами или тонкодисперсными тугоплавкими частицами, не растворяющимися в основном металле;
1.2. С неметаллической матрицей. Наиболее распространённый тип композитов. В качестве матриц широко используются полимерные, углеродные и керамические материалы. Из полимерных матриц (самый многочисленный вид композитов) наибольшее распространение получили эпоксидная, фенолоформальдегидная и полиамидная. Угольные матрицы коксованные или пироуглеродные получают из синтетических полимеров, подвергнутых пиролизу.
2. По армирующему материалу (набивке):
2.1. Стеклянные волокна. Обладают прозрачностью к радиоволнам, прочностью, электроизоляцией и низкой теплопроводностью. Это дешевый и доступный материал для применения в самых разных сферах, в том числе и в железнодорожной;
2.2. Углеродсодержащие волокна. Низкая плотность, высокий коэффициент упругости, они легкие по массе, но в тоже время очень прочные;
2.3. Борные волокна или жгуты. Имеют большую прочность при сжатии, чем волокна других материалов. Получаемые с их использованием материалы обладают отличными прочностными, износостойкими характеристиками, а также характеризуются инертностью к агрессивным средам. Но в тоже время, им свойственна хрупкость и высокая стоимость, что вводит определенные ограничения на использование;
2.4. Натуральные волокна (органопластики). Низкая плотность и вес. При этом высокая прочность. Отличное сопротивление к ударам, а также устойчивость к динамическому воздействию и нагрузкам. Прочность при изгибе и сжатии низкая;
3. По расположению (структуре) армирующего материала:
3.1. Волокна. Широко используется при производстве композитных профилей различной формы методом пултрузии;
3.2. Частицы. В этих композитах частицы, такие как керамика или металлы, встраиваются в матрицу. Они обычно обладают улучшенной термической стабильностью и износостойкостью;
3.3. Слои. Наполнение (волокна, нити, ленты) пропитанное связующим, укладывается слоями в плоскости укладки. Плоские слои собираются в пластины. Свойства получаются анизотропными (отличаются по разным направлениям прикладывания нагрузки к материалу). Именно поэтому, для правильной работы материала в изделии важно учитывать направление действующих нагрузок. Можно создать материалы как с изотропными (одинаковыми во всех направлениях), так и с анизотропными свойствами.
Можно укладывать волокна под разными углами, варьируя свойства композиционных материалов. От порядка укладки слоев по толщине пакета зависят изгибные и крутильные жесткости материала.
Для получение требуемых свойств, при разработке нового композитного материала выбирается необходимая комбинация. При этом важно учитывать сочетаемость и возможность взаимодействия друг с другом выбранных материалов. Необходимо тщательно изучить процессы, которые ожидаются на границе раздела двух (или нескольких) разнородных материалов внутри разрабатываемого композита. Важна как физическая совместимость (например, необходимый уровень адгезии или коэффициент трения у армирующего материала), так и химическая, для недопущения разъедания одного компонента материала другим.
1.4. Производство композитных материалов
Рассмотрим способы получения изделий из самого распространённого конструкционного вида композитных материалов, а именно композита с неметаллической матрицей, в качестве армирующего материала которого используются стеклянные и углеродные волокна – стеклопластик и углепластик соответственно.
Стеклопластики – это полимерный композитный материал, армированный стекловолокном, которое образуется из расплавленного неорганического стекла. В качестве матрицы часто используются термореактивные синтетические смолы, такие как полиэфир, фенол, эпоксидная смола и другие, а также термопластичные полимеры – полиамиды, полиэтилен, полистирол и тому подобное.
Стеклонить – это волокно, сформированное из стекла. В этой форме стекло проявляет несвойственные для себя характеристики – оно не трескается и не бьется, зато с легкостью принимает изогнутую форму. Для изготовления стекловолокна используется кварцевый песок, при вторичной переработке в ход идет стеклобой – это может быть стеклотара, битое стекло или забракованные стеклянные изделия, полученные в производственных условиях. Отходы стекольного производства на 100% поддаются любой переработке. Это обуславливает использование вторсырья в производстве – позволяет существенно снизить себестоимость готового материала и поддержать экологическую защиту окружающей среды.
Технология сводится к выдуванию из сырья тончайших нитей. Для этого сырьевые заготовки расплавляют при температуре 1400 градусов. Тягучая масса поступает на формующую установку и пропускается через центрифугу. В результате получается стекловата с перемешанными между собой волокнами. На финишной стадии полученный полуфабрикат пропускается через сито с микроотверстиями и выдувается под высоким воздушным давлением. На выходе получаются ровные длинные нити, которые в дальнейшем служат сырьем для создания более сложных продуктов.
Получившиеся волокна могут быть двух видов:
1) Длинные нити – растянуты на тысячи километров, их получают непрерывным методом. Через отверстия вытекают тонкие струи, охлаждаются и наматываются на барабан. Внешне такое волокно напоминает шелковую нить. В процессе вытягивания нити проходят через замасливающую установку, пропитываются клеящими веществами и пластификаторами. Такая обработка позволяет получить гибкие волокна.
2) Короткие нити – имеют длину 35—50 см, они похожи на шерсть для валяния. В основе производства лежит штапельная техника – стеклянную расплавленную массу выдувают паром или горячим воздухом.
В зависимости от толщины нитей выделяют:
– Толстое волокно – более 25 мкм;
– Утолщённое – 12—25 мкм;
– Тонкое – 4—12 мкм;
– Сверхтонкое – 1—3 мкм
Изготовление стекловолокна подчиняется действующим ГОСТам:
– для тканей конструкционного назначения – ГОСТ 19170—2001;
– для изоляционного материала – ГОСТ 19907—83.
Поверхностная плотность может быть в диапазоне 200—1800 г/кв. м, что зависит от количества нитей на 1 см2 ткани. Количество основных и уточных нитей бывает разным, как правило, от 6 до 40. Максимальная разрывная нагрузка стеклоткани разная для каждого вида, а минимальная около 1,8 Н (кгс). В соответствии с техническими характеристиками различаются и марки стеклотканей.
– Конструкционная стеклоткань. Применяется для армирования, изготовления стеклопластика, деталей автомобилей, лодок и других объектов;
– Электроизоляционная. Этот вид используют для изоляции электрических проводов, изготовления монтажных плат и так далее;
– Радиотехническая. В ее состав добавляют металлические элементы для улучшения способности отражать радиоволны и свет;
– Ровинговая стеклоткань. Для ее изготовления используют ровинги – не скрученные пучки стекловолокна, сплетенные в единое полотно. Его поставляют в больших рулонах и используют в строительстве, металлургии, автомобилестроении и других областях;
– Фильтрационная. Этот вид применяют в тех отраслях, где требуется разделить определенное вещество на отдельные фракции;
– Строительная. С ее помощью укрепляют кровлю и стены, выполняют отделочные работы.
Стеклопластики, как правило, являются листовыми пластиками. Их изготавливают методом горячего прессования полимерного связующего, смешанного со стекловолокном или стеклотканью. При этом стекловолокно (стеклоткань) является армирующим элементом. Он дает получаемому продукту повышенные физико-механические свойства.
В промышленности для выпуска изделий из этого пластика применяют несколько разнообразных полимерных смол. Больше всего среди них популярны смолы на основе полиэфиров, винилэфирные, а также эпоксидные пластики.
Изделия из стеклопластика обладают высокой прочностью, низкой теплопроводностью, высокими электроизоляционными свойствами и прозрачностью для радиоволн.
Стеклопластик – недорогой полимерный композит. Его использование оправдано в серийном и массовом производстве, в судостроении, в радиоэлектронике, в строительстве, при изготовлении оконных рам для стеклопакетов, в автомобильной и железнодорожной технике.
Впервые стекловолокно было получено случайно – на стекольном производстве случилась авария, под давлением воздуха расплавленная масса раздулась и разделилась на тонкие гибкие нити. Это стало огромной неожиданностью для инженеров, так как обычно после застывания стекло твердеет. С того момента прошло более 150 лет. За это время технология была многократно усовершенствована, но ее принцип остался неизменным.
Углепластики – это композитные материалы, которые состоят из полимерной матрицы и армирующих элементов в виде углеродных волокон. Углеродные волокна получают из синтетических и натуральных волокон на основе сополимеров акрилонитрила, целлюлозы и других.
Для изготовления композитов на основе углеродного волокна используются такие же матрицы, что и для стеклопластиков – термореактивные и термопластичные полимеры.
Основными преимуществами углепластика перед композитами на основе стекловолокна являются его низкая плотность и более высокий модуль упругости. Углепластик – очень легкий и прочный материал. Углеродные волокна и, соответственно, углепластики практически не имеют линейного расширения.
Углепластики используются в авиации, космической промышленности, машиностроении, медицине, спортивном оборудовании. Из углепластиков производят высокотемпературные узлы для ракет и скоростных самолетов, тормозные колодки и диски для авиационной техники и многоразовых космических аппаратов, электротермическое оборудование.
При получении углепластика углеродные волокна пропитываются фенолоформальдегидной смолой, затем подвергаются воздействию высоких температур (+2000° C), при этом органические вещества подвергаются пиролизу и образуется углерод. Чтобы материал был менее пористым и более плотным, операцию повторяют несколько раз.
Другой способ получить углеродный материал – прокалить обычный графит при высоких температурах в атмосфере метана. Мелкодисперсный углерод, образующийся при пиролизе метана, закрывает все поры в структуре графита. Плотность такого материала увеличивается по сравнению с плотностью графита в полтора раза.
Прессование
Процесс прессования полимерных композитных материалов заключается в пластической деформации материала при одновременном воздействии на него тепла и давления с последующей фиксацией формы изделия. Прессование композитов проводится в пресс-формах, конфигурация полости которых соответствует конфигурации будущего изделия.
Пресс-формы устанавливаются на прессах, назначение которых – создание необходимого давления прессования. Помещенный в пресс-форму холодный или предварительно подогретый материал разогревается до температуры прессования и, подвергаясь под давлением прессования деформации одномерного течения, заполняет полость формы и одновременно уплотняется.
Фиксация формы изделия происходит в результате отверждения реактопластов или охлаждения термопластов, либо охлаждения под давлением до температуры ниже температуры стеклования полимеров.
Литьё под давлением
В процессе литья под давлением формуемый полимерный композитный материал поступает в инжекционный (пластикационный) цилиндр литьевой машины, где нагревается до температуры 300—350 ⁰С в случае термопластичной матрицы и до температуры 80—110 ⁰С – в случае термореактивной матрицы.
Пластифицированный материал при поступательном движении шнека или поршня впрыскивается через мундштук (форсунку) с соплом в литниковый и разводящий каналы, а оттуда в гнезда пресс-формы, где ПКМ с термопластичной матрицей охлаждается до температуры 20—110 ⁰С, а с термореактивной – нагревается до температуры 160—200 ⁰С. В пресс-форме материал выдерживается под давлением для уплотнения, затем пресс-форма размыкается и сформованное изделие выталкивается из нее.