Installation, starting and adjustment of ventilation and air conditioning systems A Guide
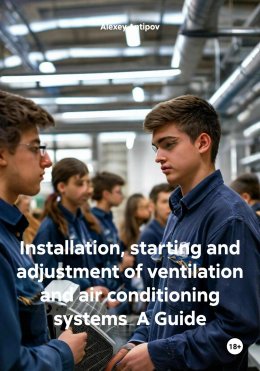
Chapter I. Motivation of a specialist in ventilation and its installations
Many people believe that the main motivation In any professional field is earning money and promotion at work. On the one hand, these are really the main Motives for people to work every day ( sometimes through force) why people go to work every day (not always the favourite one). However, we can find many people Who are unassuming and work for lower fee being completely satisfied with their job works for less salary because they are beloved with their job. So what motivates a ventilation engineer to work in this sphere?
American psychologist Abraham Maslow has identified deep motives common to all people that determine human behavior.The psychologist believed that physical survival is the first deep motive and basic human need. After he is satisfied, the person will switch to the next need. As soon as it is completed, it is the turn of the next one, there are only five main motives:
1. Physiological needs
These include air, food, drink, shelter, clothing, warm, sleep – everything that is necessary for human survival. Maslow included sex in the same group. The psychologist considered these needs to be the most important – in a situation of extreme need, a person, first of all, will think about how to survive, that is, about physiological needs. Until they are satisfied, it is unlikely that he will have other desires.
2. Safety and security
As soon as the physiological needs of a person are satisfied, the desire for security and confidence in the future come to the fore. People want to control their lives, see order and predictability around them. In society, this means the absence of direct threats to life and health, protection from natural disasters, social stability, financial security, and so on. The police, rescue services, medical and municipal institutions in general close these needs of people in society.
3. Social needs
Initially, Maslow called them "the need for love." He believed that after satisfying physiological needs and obtaining security, a person expects love and affection from other people. This block of the pyramid includes social relations: family and relatives relationship, friendship, a sense of trust in others and acceptance of a person by others.
4. Respect and recognition
Maslow divided these needs into two types: self-esteem (self-esteem, personal achievements, independence from others) and to be respected by others. A person wants to feel important both in his own eyes and in the eyes of other people. Self-esteem is directly related to a sense of self-confidence and self-worth, with self-acceptance and self-worth. Respect from others is associated with the desire to be approved by others, successful and appreciated.
5. Self-actualization
Maslow considers, that self – actualization is the ability of a person to do what he was created for. A musician feels the need to make music, an artist – to draw, a poet – to write. If a person wants to be happy, he must do what he was born for. This desire to develop one's potential is the highest need in Maslow's hierarchy. At the same time, the psychologist notes that the specific behavior into which this need will develop varies from person to person. For one, this will be expressed in the desire to become an ideal parent, for another it will be associated with sporting achievements, for a third it will be a joy to create or invent.
Fig.1. A. Maslow's pyramid of needs
To begin with, let's consider how much money you can earn constructing doing ventilation. That means we start from first stage.
Prices are given for September 2023.
HVAC Maintenance Cost by Unit Type
HVAC repair costs will differ depending on the type of unit and how extensive the repair is. Here are some average service prices based on your HVAC unit:
HVAC Service Cost by Part
If a component of your HVAC is starting to fail, you’ll need a replacement. HVAC companies will happily inspect your system and provide you with a quote for a part replacement. Here’s what you can expect:
From this table we can conclude that, any mater on Ventilation, can rise to the first step of the pyramid quite adequately. To master the remaining steps, we need to know the material outlined in the following chapters.
Questions to Chapter 1
1. Name the five steps in the hierarchical model of human needs according to the theory of Abraham Maslow.
2. Evaluate the implementation of this model on the example of work in the field of installation of ventilation systems.
3. Give an example of self-actualization in your current profession.
4. Count the advantages of the profession of an installer of ventilation systems over other professions basing on of the above model.
5. Give a comparative analysis of prices (for example, the installation of fans) from several sources on the Internet. Formulate the cost structure of the service as you see it.
Chapter II. Purpose and arrangement of ventilation systems
Purpose of ventilation systems
The state of the air is characterized by its main parameters: temperature, relative humidity, mobility (speed).
A person feels good only in a fairly narrow range of combinations of various air parameters.
The air parameters can be optimal, at which a person feels comfortable, and acceptable, at which a person's well-being and productivity of his work differs slightly from optimal. Thus, for industrial premises in the cold period of the year, the following optimal air parameters are set for medium-heavy work: temperature 18–20 °C, relative humidity 40–60% and mobility no more than 0.2 m/s.
The permissible air parameters for the same conditions have a wider range: temperature 17–23 °C, relative humidity no higher than 75% (the lower edge is not limited) and mobility no more than 0.3 m/s. In industrial premises, the maintenance of permissible air parameters is most often provided for.
Production processes may be accompanied by the release of harmful gases and vapors to humans into the air of the working area of the premises, the amount of which depends on the characteristics of the technological process, the degree of sealing of equipment, etc. The content of harmful gases and vapors in the air of the working area should not exceed the maximum permissible concentration (MPC). The maximum permissible concentration is the maximum possible amount of a harmful substance, mg/m3, per unit volume of air, which during the entire working experience does not cause diseases or abnormalities in the health of people working in these conditions, and does not affect subsequent generations. In addition, a large amount of heat, as well as moisture and dust can come from the process equipment. The person involved in the production process is a generator of heat, moisture and carbon dioxide. The heat output of one worker to the environment is 150–300 Watts or more. Every hour from 60 to 400 g of water vapor evaporates from the surface of the human body. Respiratory system produces from 20 to 40 liters of carbon dioxide.
These hazards in the form of excess heat, moisture, harmful gases and vapors enter the surrounding air and blendes in, while its temperature, moisture content, gas content, dustiness increase. This involves changes in the chemical composition and physical properties of the air.
In order to maintain normal air parameters in the premises that meet sanitary and hygienic and technological requirements, we implement ventilation, which creates an organized air exchange-removes polluted air and supplies treated (heated or cooled, humidified or drained) fresh and clean air instead.
Ventilation in most cases can provide only acceptable sanitary and hygienic conditions in the premises. The air parameters, strictly defined by temperature and relative humidity, including optimal ones, can be reached by using air conditioning systems.
Classification of ventilation systems
Ventilation systems are divided into supply systems that supply fresh air to the premises, exhaust systems that remove dirty air from the premises, and air or air-heat curtains that prevent the penetration of cold air through the entrance or doors of buildings during the cold season.
Both supply and exhaust ventilation systems can be general and local type. General exchange systems are designed to supply and remove air evenly throughout the serviced room, to create an air environment with approximately the same parameters throughout the entire volume of the working area. Local exhaust systems remove the air in the places of formation of hazards from technological equipment, preventing the hazards from spreading throughout the entire volume of the room, polluting the entire air of the workshop. Local supply systems supply fresh air near workplaces, create an air shower or oasis – a restricted area in the production room where the parameters of the air environment meet sanitary and hygienic requirements.
Local exhaust ventilation is much more effective than central or general exchange ventilation, since it removes air from the places of formation of hazards with a higher concentration of them, does not allow the hazards to spread freely throughout the room, but such ventilation is not always feasible.
According to the method of air movement, all ventilation systems are either natural or mechanical.
In natural ventilation systems, air movement occurs due to the difference in densities of internal (heated and lighter) and external (colder and heavier) air.
In mechanical ventilation systems, air is moved by a fan or other equipment (a smoke pump, a blower, an ejector, etc.) driven by an electric motor. Mechanical systems are used much more often than natural ones, since the area of action of mechanical systems is much larger, and the cross sections of air ducts are smaller than in natural ventilation systems of the same capacity, due to higher air velocity. So, in the air ducts of natural ventilation systems, the air velocity is 0.5–2 m/s, and in the air ducts of mechanical systems 4–20 m/s.
During the operation of ventilation of any kind in the room, the air is forced to be changed. The ratio of the amount of fresh air supplied to the room for 1 hour to the internal volume of the room is called the multiplicity of air exchange. In real conditions, the multiplicity of air exchange can vary from 0.5 to 20 or more.
In addition to the designed air exchange carried out by ventilation systems, air can enter the premises by infiltration through leaks of windows, walls, doors, gates, etc. due to gravitational (natural) pressure and due to wind pressure. In the same way, air can be removed from the room.
If there are no harmful emissions in the room, then the supply ventilation systems are carried out in such a way that they take part of the air from the outside, and part from the room. This secondary use of air from the room for supply systems is called recirculation. It allows you to reduce the temperature difference between the supply air and the indoor air during the cold season, increase the relative humidity of the air and, most importantly, save heat (in winter) or cold (in summer).
Installation of ventilation systems
Natural ventilation systems can be ductless if air passes only through open apertures in external fences, or are ducted when air moves through ducts.
The operation of natural ventilation largely depends on the action of the wind. The wind, running into the building, creates an overpressure zone on the windward side, and a negative pressure zone on the leeward side. Controlled natural air exchange in the workshops of industrial buildings is called aeration. Such buildings are equipped with lanterns with shutters (transoms) that can be opened manually or by special mechanisms. The same opening valves are provided with window openings in the outer walls. By opening them partially or completely, you can create the required air exchange. Aeration is calculated only for the effect of gravitational pressure, since wind pressure is episodic and, as a rule, increases air exchange. Aeration is usually provided in industrial buildings with significant heat emissions.
The advantage of aeration is that air exchange is created without the help of fans, without consuming electricity. However, aeration provides only general exchange ventilation and does not provide cleaning of supply and exhaust air.
Mechanical ventilation systems can provide local ventilation.
The supply systems of mechanical ventilation supply purified air with a set temperature and, in some cases, humidity to the working area of the workshop to ensure the required sanitary and hygienic conditions for people and equipment inside the building. Mechanical ventilation exhaust systems remove dusty and polluted air, purifying it if necessary before being released into the atmosphere.
Supply ventilation systems consist of the following main elements: an air intake device, an intake chamber, which includes an insulated valve, a filter, an air heater (heater) and the fan, the network air ducts and air distributors, as well as regulating devices (diaphragms).
The air intake device is located in the least dusty area of the site, but as close as possible to the supply chamber or on the roof. At the entrance to the air intake shaft or channel, a louvered grille is installed to protect against atmospheric precipitation and from foreign objects. An air intake shaft or channel is made in building structures made of brick or concrete. Sometimes one intake duct feeds several supply systems with external air.
An insulated valve (flap) with manual or electric drive is installed between the air intake device and the filter of the supply chamber. When the fan is not working, the valve must be closed to protect the supply chamber equipment from outside cold air.
The supply chamber consists of a louvered grate, a filter for air purification, heaters for heating it and a fan with an electric motor. Supply chambers can be installed on a foundation or a platform, or suspended from ceiling structures of coatings. No fencing is required for these cameras.
Air ducts of supply systems are usually made of thin – sheet galvanized steel roofing with a thickness of 0.35–1.4 mm. The air ducts can be of round or rectangular cross-section. Metal ducts are quickly mounted, are strong enough and have good tightness. When laying air ducts under the floor, they are made of concrete or brick.
Air distributors (supply nozzles) are designed to distribute supply air. The supply air can be supplied to the working area; for this, the air distributors must have a short torch and a slight velocity of the outgoing air to eliminate the feeling of a draft. When air is supplied to the upper area of the room, on the contrary, the air outlet speed should be higher so that the fresh air stream reaches the working area.
Air distributors are installed in suspended ceilings, some are mounted at a low height above the working area.
A type of supply ventilation systems is air shower, which provides a concentrated flow of air to the workplace. A workplace is a platform with a diameter of 1 m, on which the worker is at least 4 hours per shift or 2 hours continuously. Such an air supply is necessary for intensive thermal (from 300 to 3000 W/m2 or more) irradiation of workers, or for open production processes with the release of harmful gases and vapors, when it is impossible to arrange local shelters. Actually, the scheme of air douching does not differ from the supply ventilation system, but instead of air distributors, showering rotary nozzles are installed.
Air and thermal-air curtains are designed to protect the gates and open entrances of industrial buildings from the intake of cold air in winter. There are two types of curtains: sliding, in which a flat jet of air is supplied either from below or from the sides of entrances and gates at some angle towards cold air, and mixing, when air from the building is supplied to the vestibule between the double entrance doors. Mixing curtains are used in administrative and public buildings, in passageways, etc. Curtains in which the air is preheated in an air heater are called thermal-air, and curtains that supply air without heating are simply air type.
Air-heating units with full or partial air recirculation are often used in air heating systems.
General exchange exhaust ventilation systems usually remove air from the upper, less often from the middle zone of buildings. Before removal, the air in general exchange exhaust systems usually does not undergo cleaning. General exchange exhaust systems can be channelless if the air is removed by roof fans that are installed on the floors, and ducted. In ducted exhaust ventilation systems, air is sucked into air intake apertures or grilles, it is fed through the ducts to the fan and, after passing the exhaust shaft, enters the atmosphere. To protect the exhaust shaft from atmospheric precipitation, an umbrella is installed above it, and the air ducts are blocked with a flap when the fan is not working.
Local exhaust ventilation systems are designed to take harmful emissions from the places of their formation with the help of shelters or local suction, transport polluted air, clean it in filters or dust collectors and release it into the atmosphere. Local suction and shelters have the most diverse design and shape: these are umbrellas, fume hoods, full shelters, side and ring suction at baths and shaft furnaces, suction panels, casings, etc.
Many harmful substances released during technological processes actively affect local suction pipes, air ducts, fans, filters, causing their severe corrosion, in addition, they can be explosive and fire-hazardous. In these cases, air ducts and other devices in contact with an aggressive environment are made of materials that are not subject to intense corrosion by the moving medium (corrosion-resistant alloy steels, aluminum, titanium. metal, vinyl, polyethylene, etc.), or apply special coatings of steel ducts with acid- and alkali-resistant dyes, enamels and varnishes. In such systems, fans and other equipment are installed in an intrinsically safe protected design.
Questions for chapter 2
1. Name the main parameters of the air environment.
2. What is the main purpose of the ventilation system?
3. In which cases the use of natural ventilation systems is justified.
4. What is the advantage of mechanical ventilation systems?
5. What is the name of the process of heat recovery of the removed air, what are its technical and economic advantages?
6. What material is used to produce ventilation ducts most often?
7. What, in your opinion, is affected by the thickness of the metal in the production of air ducts?
8. In which cases air showering is used?
9. Name the main processes of air treatment in the supply ventilation system.
10. In which cases a special design of air ducts and ventilation equipment is used?
Chapter III. Equipment of air ventilation systems
As indicated above, the required state of the air environment in the premises is maintained by general exchange ventilation methods by pumping clean ventilation air into the premises with the necessary temperature-humidity parameters and removal of air that does not meet regulatory requirements. In accordance with this, general exchange ventilation systems should include equipment and devices for intake of outdoor air, its processing, transportation and distribution around the premises, as well as for the removal of exhaust air.
3.1. Air intake and air discharge devices
These include air intake and air discharge devices in mechanical ventilation systems, which are made in the form of holes in the fences of buildings, attached or freestanding shafts. When air is taken from above, the air intake devices are placed in the attic or upper floor of the building, and the channels are removed above the roof in the form of shafts.
For aeration, air intake and ejection devices are made in the form of rotating transoms, opening lanterns, windows or other overlapping apertures in the fences of buildings.
The location and design of the air intake devices are selected taking into account the cleanliness of the intake air and the satisfaction of architectural requirements. Thus, air intake devices should not be located near sources of air pollution (emissions of polluted air or gases, chimneys, kitchens, unpaved roads, etc.).
Air intake apertures should be located at a height of at least 2 m from the ground surface and closed with louvered grilles (in the green zone – at a height of at least 1 m).
To protect the premises from outside cold air during standby of the ventilation through ventilation ducts, air intake and air discharge devices are equipped with multi-leaf insulated valves with manual or mechanical drive. In the latter case, the valve is blocked along with the fan closing the apertures. At low temperature of the outside air, the valves are supplied with an electric heating system in order to protect their flaps from freezing. Electric heating is turned on for 10–15 minutes before starting the fan (Fig.2).
Fig.2. Electric air valve
The outer walls of exhaust ducts and shafts are insulated to avoid condensation and ice of water vapor from the extracted moist air. The air velocity in the supply channels and shafts is supported between 2 and 5 m/s, in the channels and shafts of exhaust devices: 4–8 m/s, but not less than 0.5 m/s, including for natural ventilation.
3.2. Ventilation chambers
The main ventilation equipment of supply and exhaust installations, as a rule, is installed in special rooms called ventilation chambers. Supply chambers in public, administrative, residential buildings are usually designed on the ground floor or in the technical underground. Exhaust chambers should be located in the upper part of the building. In multi-storey buildings with a large number of ventilation systems, ventilation chambers are arranged in technical floors.
In buildings with a large number of ventilation systems (more than 5), a room for equipment repair is provided. The operation of ventilation systems is controlled from special remote controls using automation and remote control devices.
3.3. Fans
The fan is a mechanical device designed to move air through the ducts of ventilation systems, as well as to carry out direct air supply to the room or suction from the room, and creating the pressure drop necessary for this (at the inlet and outlet fan). According to the design and principle of operation, fans are divided into:), radial (centrifugal), diametral (tangential) (Fig.3).
Fig.3.Fan designs
Currently, modifications of radial fans are used – direct-flow, disk, vortex, tornado (Fig.4).
Fig.4. Modifications of radial fans
Fans are evaluated by specific speed, which relates the rotational speed and pressure.
We divide fans into three groups, depending on the magnitude of the total air pressure they create: low pressure (up to 1 kPa), the maximum circumferential speed of such wheels does not exceed 50 m/s; medium pressure (up to 3 kPa), the maximum circumferential speed reaches 80 m/s; high pressure (up to 12 kPa), the circumferential speed of the impellers is more than 80 m/s.
The separation of fans by pressure is conditional, since any high-pressure fan with a decrease in the speed of rotation can be used as a medium-pressure fan.
In the direction of rotation of the impeller (when viewed from the suction side), the fans can be of right rotation (the wheel rotates clockwise) and left rotation (the wheel rotates counterclockwise).
Depending on the composition of the transported medium and operating conditions, fans are divided into: conventional – for air (gases) with a temperature of up to 80 °C, corrosion-resistant – for corrosive environments, heat-resistant – for air with a temperature above 80 °C, explosion-proof – for explosive environments, dust-proof – for dusty air (solid impurities in the amount of more than 100 mg/m3). According to the method of connecting the fan impeller and the electric motor, the fans can be: with a direct connection, with a connection on an elastic coupling, with a V-belt transmission, with an adjustable stepless transmission.
At the place of installation, fans are divided into: conventional, mounted on a special support (frame, foundation, etc.), ducted, installed directly in the duct, roof, placed on the roof.
The main characteristics of the fans are the following parameters: air consumption (m3/h), total pressure (Pa), rotation speed – rotations per minute (rpm), power consumption spent on the fan drive (kW), EFFICIENCY – the efficiency of the fan, taking into account mechanical power losses due to various types of friction in the fan working bodies, volume losses as a result of leaks through seals and aerodynamic losses in the flow part of the fan, the sound pressure level (dB).
3.4. Supply installations
The supply units (Fig.5) filter fresh air, if necessary, heat it (in the cold season) and supply it to the duct system for subsequent distribution around the premises.
Fig.5. The supply unit
Inlet ventilation units consist of a housing in which are mounted: filter, water or electric heater, fan, automation system, sound insulation material,
Conditionally, Inlet installations can be divided into several types:
by type of heater (with an electric heater or with a water heater), by air consumption (up to 200–3000 m3/h – mini-supply installations, more than 3000 m3/h – central supply installations), by design (for vertical installation, for horizontal mounting, universal)
The automatic control system of the supply unit allows you to gradually or smoothly adjust the thermal power of the electric heater. If a water heater is used in the supply unit, then the automation has a more complex design, since in this case it is necessary to provide additional protection against freezing of the heater in winter.
In ventilation systems with supply installations, the following additional elements can be used: air intake grilles, a valve for supply air (with an electric drive or manual drive), mufflers, devices for adjusting air flow in rooms, air distribution devices (diffusers, grilles, plafonds).
Structurally, the chambers are a monoblock structure and can be equipped with automatic control of various levels of complexity from simple functions such as START, STOP, OPEN-CLOSE VALVE, to programmable control of parameters (room temperature, performance, temperature inside the chamber, etc.) along a continuous circuit.
The supply chamber includes the following elements:
A double-sided suction fan, which is attached to the frame traverses through rubber vibration isolators. The frame is made of aluminum profiles and connecting corners.
Insulated panels made of galvanized steel on the outside and inside. Foam insulation is laid in the panel as a heater and sound insulator. For tightness, a self-adhesive sealer is laid between the panels and the frame. On one side of the camera, for ease of maintenance, the panels are made quick-detachable, for which they are equipped with rotary clamps.
Heater (water heater or electric heating elements).
Soft insert made of rubberized fabric with flanges on both sides. The flanges are made of a galvanized tire connected by corners.
Quick-release air filter.
Insulated air valve with electric drive.
To create a balance of the incoming and outgoing air from the room, exhaust ventilation is used, which can be represented by:
• autonomous axial fans installed directly in the wall;
• roof fans installed on the roof;
• centrifugal fans mounted on brackets in the wall or on metal roof structures;
• duct fans in a shell-shaped housing or in a box-shaped housing installed in a network of air ducts (have a nozzle at the inlet and a diffuser at the outlet, and in the case of installing a two-way suction fan – two at the inlet and one at the outlet).
• exhaust ventilation units equipped with fans, flexible inserts, control valves and assembled in a single housing (Fig. 6).
Fig.6 Exhaust system
Supply and exhaust ventilation systems can significantly reduce heating costs by using heat recovery. The heat removed from the room air can be used to heat the supply air in special heat exchangers called recuperators.
Such a system, using a cross-flow recuperator and made in the form of a monoblock, is characterized by a high efficiency of heat recovery, reaching 70%, and provides at least a twofold reduction in operating costs for air heating due to heat recovery (Fig.7).
Fig.7. Supply and exhaust system with recovery
Heat recovery units are designed for the organization of supply and exhaust ventilation in comfortable air conditioning systems, i.e. they change the temperature and humidity of incoming fresh air taking into account the climatic conditions inside the serviced room.
The cross-flow plate regenerative heat exchanger is made of a heat-conducting material having the property of selective permeability with respect to water molecules (practically the membrane is impermeable with respect to molecules of other gases and substances). Due to this, the difference in the partial pressures of water vapor in the outdoor and exhaust air leads to the transfer of moisture from one stream to another. In the cold season, water molecules from the wetter exhaust air penetrate through the membrane into the outside air stream, humidifying it. In the warm season, water molecules from the wetter outdoor air penetrate into the exhaust air stream, preventing excessive humidification of the room.
3.5. Heaters
To heat the air in the supply ventilation units, heaters (air heaters) are used.
Fig.8. Water heater
High-temperature water or steam is used as a heat carrier for heaters. When the heating liquid is water, the heaters are marked as HW, when steam is marked as HS.
Heaters designed to work with a steam coolant are manufactured single – pass, with a water coolant-both single-pass and multi-pass. In single-pass heaters, the coolant passes through the entire bundle of tubes simultaneously from one collector to another, and in multi-pass collectors are separated by internal partitions that repeatedly change the direction of movement of the coolant, which increases the speed of water movement through the tubes and, as a consequence, increases the heat transfer of the heater. The connection of fittings in single-pass heaters is diagonal, and in multi-pass ones it is one-sided (Fig. 9).
Fig. 9. The flow diagram of the coolant in the heaters:
a – single–pass; b – multi-pass
Fins in the form of plates (plate heaters) or wound steel tape (spiral-wound heaters) are placed on the tubes to increase the contact area with the air passing through the heater. The outer fins are galvanized to reduce corrosion and better contact of the fins with the tubes. Fittings for the coolant are welded into the collectors, and to protect the fins from damage from the side, side shields are welded between the collectors. Flanges are used to connect the heater to adjacent elements of the ventilation system.
The arrangement of the tubes with the heating liquid can be consistent in the direction of air movement (corridor), staggered and offset along the corridor (most effectively). The tubes themselves can be either round or flat-oval in cross-section.
The best thermal engineering indicators have spiral-rolled bimetallic three- and four-row heaters for both steam (single-pass) and water (multi-pass) heater. The tubes for the heat carrier in these heaters are steel, the fins are rolled from aluminum.
Heaters are often grouped into several pieces, both with a parallel installation through the air, and with a sequential or combined one. If the heat carrier is steam, then the heaters are installed with a vertical arrangement of tubes and steam supply to the upper branch pipe; if the heat carrier is water, then the position of the tubes should be horizontal, which ensures the removal of air when filling the heaters with water and draining water from it when the system stops working.
Electric heaters are also available (Fig.10).
Fig.10. Electric heater
Electric heaters consist of a steel casing with tubular heating elements: 1.6 or 2.5 kW each. To increase the heating surface area, the heating elements have ribs with a diameter of 42 mm. Electric heaters can work both in manual and automatic mode, maintaining a constant temperature of the air at the outlet or in the room.
3.6. Duct heaters
The duct heater is used to heat the supply (outdoor) air in the ducts (conventional circular section). In central ventilation systems, duct heaters are used as auxiliary heaters, and in decentralized ones – as the main air heaters.
The heater body is made of galvanized steel. Air heating is carried out by heating elements. It is mandatory to have protective and regulating thermostats, which provides the product with high safety and the ability to function in automatic mode at the same time.
Channel heaters are equipped with two thermostats for overheating protection: heat-protective with automatic restart (operating temperature +50 °C) and fire-fighting with manual restart (operating temperature +110 °C). Channel heaters are designed for a minimum air flow velocity of 1.5 m/s and a maximum operating temperature of 40 °C of the outgoing air.
3.7. Air coolers
Duct air coolers (Fig. 11) are designed for cooling and dehumidification of supply, recirculating air or a mixture thereof in ventilation and air conditioning systems of industrial, public or residential buildings.
Fig. 11. Air cooler with ducted water and freon coolers
Water or non-freezing mixtures can be used as a refrigerant in ducted water coolers. The maximum allowable liquid pressure in them is 1.6 Mpa.
Freons are used as a refrigerant in ducted freon coolers. Upon delivery, the heat exchangers are filled with inert gas, which must be removed during connection to the refrigeration circuit.
The design of the cooler is a housing made of galvanized steel, inside which a heat exchanger, a drop trap and a pallet are installed.
The heat exchanger is made of copper tubes with aluminum fins arranged in a staggered order.
The freon cooler is distinguished by the design of the distribution unit ("spider") and the specifics of the refrigerant supply.
The collectors of the freon heat exchanger are made of copper tubes.
The drip trap (Fig. 12) is a set of special plastic plates that effectively trap condensate and collect it into a tray located in the lower part of the cooler body.
Fig. 12. The shape of the droplet trap plates.
The pallet is additionally thermally insulated and equipped with a discharge pipe for draining condensate
When installing the air cooler, it is necessary to ensure its horizontal position.
3.8. Filters
Filters are divided into three classes according to their effectiveness. Class I filters trap dust particles of all sizes (the cleaning coefficient is not less than 0.99), Class II filters – particles of more than 1 micron (cleaning coefficient is more than 0.85), class III filters – particles of more than 10–50 microns (cleaning coefficient is not less than 0.60).
3.9. Noise suppression equipment
The noise level generated by ventilation systems is an essential criterion of ventilation quality. The sources of noise in ventilation installations are fans and electric motors, as well as the movement of air in the ducts and its exit from the holes. Two types of noise are considered: aerodynamic and mechanical.
The reasons for the appearance of aerodynamic noise in fans are: the formation of vortices and their periodic disruption from the blades of the impeller, local air flows at the entrance to the wheel and at the exit from it, leading to unsteady flow around the blades of the wheel, perturbation of the medium by rotating blades. Mechanical noise occurs in bearings, in the drive, in the installation sites (fasteners) of the ventilation unit on building structures, etc. The degree of noise increases with insufficient balancing of the fan impeller.
Of all the sources of noise generation, the dominant ones are fans that create aerodynamic noise. The noise generated by the ventilation system can be reduced by the following measures: installation of fans with the most advanced acoustic characteristics, in particular, fans with blades bent backwards; the choice of fans with the highest efficiency (not less than 0.9 of the maximum), with a minimum angular velocity of the impeller (not higher than 30 m/s), i.e. fans with a small diameter of the impeller and a small number of revolutions (at the same time, you should not overestimate the pressure against the calculated one, since this causes an increase in noise level); careful balancing of the impeller.
Noise reduction along the path of its propagation is achieved by limiting the speed of air movement in the ducts or lining the inner surfaces of the ducts with a sound-proofing material.
In order to reduce the transmission of fan vibration to the ducts, the latter must be connected to the fan nozzles using soft inserts made of rubber, rubberized tarpaulin.
Vibration noise reduction is achieved by installing ventilation units on vibration isolators. Standard designs of spring and rubber vibration isolators are used (Fig. 13).
Fig. 13. Vibration Isolator
With the number of revolutions of the impeller up to 1800 rpm, it is recommended to use spring vibration isolators, characterized by stability of elastic properties, allowing large deflection and weakening vibrations even at very low frequencies. With large numbers of revolutions, the use of rubber vibration isolators is allowed.
In order to reduce the transmission of vibration to the structure of the building, fans should be mounted on their own concrete foundations on the ground. In the case of installation of ventilation units on the load-bearing structures of buildings, the plates or beams on which they are located must be mounted on vibration-absorbing supports.
The reduction of the noise level transmitted from the ventilation chamber to adjacent rooms is achieved by the installation of fences around it from structures with increased sound absorption, as well as the use of sound-absorbing linings in chambers and rooms. In ventilation chambers, it is possible to arrange "floating" floors consisting of layers of fiberglass plates, soundproof strips, etc.
. For active muffling of aerodynamic noise, mufflers are widely used in ventilation systems, the principle of operation of which is based on the conversion of sound energy into thermal energy by friction.
By their design, silencers are divided into tubular, honeycomb, plate and chamber silencers (Fig. 14).
Fig. 14. Muffler designs
a – lamellar with extreme plates; b – lamellar without extreme plates; c – tubular rectangular section; d – tubular circular section; e – chamber;
1 – muffler casing; 2 – sound – absorbing plate; 3 – air channels; 4 – sound-absorbing lining; 5 – internal partition;
A – the distance between the plates; B – the thickness of the plates; H, Hx – the dimensions of the duct; C -the thickness of the lining of the duct; D – the diameter of the duct
By design, silencers are divided into tubular, cellular, plate and chamber.
Tubular silencers are made round, rectangular. Cellular and plate silencers are made only rectangular. As a sound-absorbing material, soft mats made of superfine fiberglass with a thickness of 100 mm are used for tubular and cellular silencers and with a thickness of 100, 200 and 400 mm for plate silencers. To prevent the entrainment of the fiber with the air flow, the sound-absorbing layer is protected with fiberglass and metal mesh or perforated sheets with a perforation of at least 20%.
The plate silencer is a box made of a thin metal sheet. A tubular silencer is made in the form of two round or rectangular pipes inserted into one another. Tubular silencers are used on air ducts with a diameter of up to 500 mm.
Currently, active silencers have been developed that carry out broadband active noise suppression (especially effective at low frequencies). Noise neutralization is carried out by introducing antiphase noise.
3.10. Check valves
Check valves are used to allow air to pass in one direction and prevent it from moving in the opposite direction. They are available in two of the simplest modifications: the "butterfly" type and the "inertial lattice" type (Fig. 15).
Fig. 15. Check valves
The butterfly valve is made of galvanized steel, has two spring-loaded lobes, and can be installed in any position.
A petal check valve of the "inertial grid" type with light plastic blinds inserted into a galvanized steel box can only be installed on horizontal air ducts, under the action of the air flow in the permitted direction, the petals rise, in all other cases they are lowered.
One of the main characteristics of check valves is the maximum possible air velocity.
Check valves are used to prevent air flow: when several supply units are operating on the same network; when installing a backup supply or exhaust fan; when connecting several exhaust systems to one exhaust shaft.
They are also installed to prevent backflow of air when exhaust air is released onto the facade or in front of roof fans.
3.11. Air curtains
Air curtains (without air heating) they are arranged between rooms with the same or similar thermal conditions. They are used to prevent access of air from some rooms in which harmful vapors or gases are released to others.
The principle of operation of air-heat curtains is as follows: air is taken from the upper area of the lobby, heated in heaters up to 50 °C, fed by a fan into the air distribution chamber and then released through the uniform distribution duct at the door. The air is discharged through cracks or holes in the duct. The resulting jet creates a vertical air curtain. The air can be released from the bottom at the door or from the side to the desired height. Air is supplied to the air curtain from the supply ventilation without additional heating.
According to the principle and effect of the curtain, there can be gate and mixing types. In the first case, the curtain maximally or completely prevents (blocks) air access to the enclosed space; the air velocity from the installation to create such curtains should be high (up to 25 m/s). Such curtains are arranged at low outdoor temperature and frequent opening of doors. In mixing type installations, the rushing cold air is mixed with the heated air of the heat curtain. As a result, warm air enters the room through the door and the curtain, which does not create a feeling of cold blowing.
Questions to Chapter 3
1. What is the reason for the location of outdoor air intake devices in ventilation systems?
2. Name the main types of fans by type and design.
3. What is the reason for the mandatory installation of the filter in front of the heat exchange equipment (heaters and coolers)?
4. Give an example in which cases it is advantageous to use electric air heaters.
5. What are the advantages of using water heaters?
6. Why the range of air velocity in heat exchange equipment is strictly limited?
7. What is the fundamental difference between water (water-glycol) and freon air coolers?
8. What measures are envisaged to reduce noise in ventilation systems?
9. Which device is used to prevent air flow when the fan is turned off?
10. In which places of the building are provided air heat curtains with heated air?
Chapter IV. Ducts and Fittings
4.1 Air ducts of ventilation systems
According to the type of section, the ducts are divided into round, square or rectangular. Circular air ducts are much stronger than rectangular ones, and their manufacture is less laborious.
However, circular air ducts often do not fit into the interior of public and civil buildings. In addition, in a confined space (under false ceilings, etc.), as a rule, only rectangular air ducts can be used.
According to the manufacturing method, the air ducts can be folded or welded. (Fig. 16.).
The first ones are connected with seam seams. The thickness of the metal for such ducts should not exceed 2.0 mm (if aluminum is used) and 1.0 mm (if corrosion-resistant steel is used).
The welded air ducts are connected by an overlap weld. The thickness of the metal with this type of connection is allowed in the range of 1.2 -3.0 mm.
Fig.16. Types of seam and welded joints of metal ducts:
1 – on a simple recumbent seam; 2 – on a double–cut seam; 3 – on an angular seam; 4 – on a transverse seam; 5 – on a seam with a latch; 6 – with a connecting bar; 7 – on zigs; 8 – butt; 9 – butt–to–butt with flanging; 10 – lap; 11 – corner
This type of duct is classified as dense.
All the various ventilation systems are assembled from only four standard parts.
The first is pipes with a length of 2000 mm or 2500 mm, depending on the metal used.
The second is from water, usually consisting of two or three segments and two glasses with an average radius of curvature equal to the diameter (Fig.17). They are used for general exchange ventilation systems.
Fig. 17. Outlet for air ducts
The third is rectangular bends, which are characterized by only two neck radii: 150 mm (for bends with a side less than 1000 mm) and 300 mm (with a larger size).
The fourth is the tees (branch nodes) of circular cross section. They exist in 3 versions:
– normalized, they are characterized by low coefficients of local resistance, but are laborious to manufacture;
– direct embedding;
– rectangular tees, they are usually equipped with one-sided unified transitions, which allows you to establish a constant ratio of the duct route from the wall along which it is laid.
According to the material used for the manufacture of air ducts, they are divided into several groups:
1. Folded air ducts made of thin-sheet galvanized steel, up to 1 mm thick (without painting).
2. Folding air ducts made of thin-sheet black steel, up to 1 mm thick (with subsequent painting inside and outside).
3. Welded air ducts made of sheet steel, 1.2- 3.0 mm thick (with subsequent painting with primer).
4. Seam and welded air ducts made of corrosion–resistant steel, thickness from 0.5 mm to 3 mm (usually grades X18N9T) – without painting.
5. Folding air ducts made of titanium (ρ = 4,500 kg/m3), which have the highest corrosion resistance when moving an aggressive medium.
6. Folding ducts made of metal plastic, clad on one or both sides with PVC or PVC film. With a one-sided coating, the film must be inside the duct, in contact with an aggressive environment.
The connection of individual parts of round air ducts to each other is performed by flanging bandages (with a diameter of up to 800 mm) or on flanges made of angular steel (with large diameters).
The connection of rectangular air ducts with a side less than 1600 mm is performed on profiled tires fastened with 4 bolts at the corners. If the side dimensions exceed 1600 mm, additional latches are used.
For conventional general exchange systems, it is preferable to use folded air ducts made of galvanized steel. Welded air ducts are installed with increased density requirements (smoke extraction shafts, air ducts passing through rooms with explosion hazard category A and B) and air movement with a temperature above 80 °C.
Flexible reinforced air ducts are widely used to avoid difficult fitting when connecting from mains to air distributors and grilles.
One of the latest solutions in the field of air distribution is textile air ducts. They are inflated by the flow of air and evenly distribute it along their entire length. In addition to noise reduction, textile ducts have the ability to trap all dust particles larger than 5 microns. They can be used in rooms with a high frequency of air exchange, without creating local areas with increased air mobility, as is the case with jet distribution.
This type of duct combines two devices – the duct itself and the air distributor.
There are several options for the operation of a textile duct. The air supply to the room can be carried out through its entire surface (in this case, airtight fabric channels made of 100% polyester are used) or through special holes made in the duct material (an impermeable fabric with perforated injector holes is used). Mixed versions are also used. The air flow velocity inside the airtight material does not exceed 0.01–0.5 m/sec, the air velocity coming out of the cracks is 4–10 m/sec, through perforated holes (injectors) is 7–13 m/sec.
Cylindrical fabric ducts are the most common. They are convenient if you need to provide intensive air exchange, preventing drafts. Semicircular air ducts are used in rooms with low ceilings, for example, in catering establishments, non-food stores, hotels, etc. Air ducts in a quarter-section of a circle can also be used, installed around the perimeter of the room.
Installation of steel ducts in rooms with high ceilings is quite laborious and time-consuming. The use of textile air ducts greatly facilitates the work. Sections of air ducts (usually 5 m long) are connected to each other with the help of zippers. The air ducts are suspended using stretched cables or rails. In the latter case, the fastening is more rigid, and the duct retains its shape even without air supply. When condensation occurs, a nutrient medium is formed that promotes the development of microorganisms. Textile ducts can be easily dismantled, washed or cleaned. They are produced with a diameter of 100 to 1000 mm and a length of up to 100 m, as well as various densities that allow changing the air supply from 160 to 500 m3 / g * m2 at a static pressure inside 100 Pa.
When transporting hot gases with a temperature of more than 100 °C in ventilation systems, the thickness of the steel walls of the air ducts should be 1–2 mm. To transport air with an admixture of toxic gases and vapors, air ducts must be made of certain materials, depending on the composition of the gases (steel with a thickness of at least 0.7 mm, aluminum, vinyl, etc.).
In ventilation systems of residential, public and administrative buildings, as well as office and auxiliary premises of industrial enterprises, air ducts made of slag-alabaster, cinder-concrete, reinforced cement and plastic plates, bricks, concrete, etc
. are used for portable ventilation installations rubberized, as well as metal flexible hoses.
When laying rectangular vertical air ducts, they try to make the most of the internal walls, in which appropriate channels are left for this purpose. If this is not possible, side channels and shafts are mounted to the walls.
In addition, spiral-wound metal air ducts are used in construction practice, as well as plastic air ducts that resist corrosion (made of vinyl, polyisobutylene, etc.). Their disadvantage lies in the fact that they can only be used at a temperature of transported air no higher than 70 °C.
In addition to these modifications, the ducts can be flexible, semi-flexible, thermally insulated, and also acting as a muffler.
4.2. Metal air ducts
Most often, metal ducts are used in air conditioning systems, which have great strength and resistance to fire.
They are made of galvanized or stainless steel.
Spiral-lock round (with a folding connection). They are made of steel tape with an anti-corrosion coating 0.5–1 mm thick, about 130 mm wide. They have increased rigidity compared to straight-seam ducts, there is no length restriction, aesthetic appearance, high seam density. The disadvantages include the fact that the seam takes about 15% of the metal from which the duct is made.
Spiral-welded round. They are made of steel tape with an anti-corrosion coating 0.8–2.2 mm thick, about 400–750 mm wide. The joints are welded overlap. Spiral-wound air ducts have less metal consumption compared to spiral-lock air ducts, there is no length restriction, high seam density. However, they cannot be made from steel thinner than 0.8 mm.
Rectangular straight-folding air ducts. They are made of steel sheet, it is desirable to place the seam on the bend so that it serves as an additional stiffener. Such ducts are easier than round ones to place in a space with a limited height, they fit better into the interior of the building. Rectangular ducts have greater aerodynamic drag than circular ducts with similar performance.
Round straight-folding air ducts. According to the manufacturing method and material, they are similar to rectangular air ducts, they differ only in a circular cross section.
4.3. Metal-plastic air ducts
Metal-plastic air ducts consist of two layers of metal, between which foam plastic is laid. Usually such a construction is used: foamed plastic 2 cm thick, located between layers of corrugated aluminum 80 microns thick. They have a small mass with high strength. They have a smooth surface, aesthetic appearance, do not require additional thermal insulation.
4.4.Non-metallic air ducts
Non-metallic air ducts are made of synthetic materials: polyethylene, fiberglass, etc.
Polyethylene air ducts: are usually used in supply ventilation systems. When the fan is turned on, the duct (in the form of a sleeve) is inflated with air.
Fiberglass ducts: usually used to connect the fan and air distributors. They are stretched on a metal frame.
Vinyl plastic air ducts: used when moving air containing acid vapors, etc., causing corrosion of steel. The thickness of the vinyl plastic is 3–9 mm, connected by welding.
Non-metallic air ducts are resistant to corrosion, they can be bent in any plane and at any angle.
4.5. Flexible air ducts
Flexible ducts of circular cross-section, lightweight, do not need special turns, as a result of which the duct has fewer connections, which simplifies installation. However, flexible ducts create a large aerodynamic drag, which may be excessive with an extended network, so they are often used as connecting pipes of small length. Flexible ducts are divided into:
• Flexible aluminum ducts without heat and noise insulation;
• Aluminum ducts with polymer coating without heat and noise insulation;
• Highly flexible polyvinyl chloride ducts;
• Highly flexible insulated air ducts consisting of two layers of polyvinyl chloride coated with polyamide fabric. A flexible steel wire spiral is located between the two layers.
• Semi-rigid aluminum ducts with thermal insulation;
• Flexible heat-insulated sound-absorbing air ducts. They consist of:
– Micro-perforated air duct made of high-strength metallized polymer;
– 25- 50 mm of thermal insulation layer with a density of 16 kg/m3;
– An outer coating made of aluminum seamlessly reinforced with fiber.
These ducts have excellent noise reduction performance in the low frequency range. To reduce the possible consequences of the use of mineral fibers on human health, the inner sleeve has minimal perforation, a special acoustic film is placed between the inner sleeve and the insulation layer. This reduces the probability of fiber entrainment at normal air flow speeds to almost a minimum.
Condensation formation, safety, noise, energy saving – these are the criteria that should be taken into account when choosing a material for thermal insulation of air ducts.
4.6. Thermal insulation
Thermal insulation of air ducts performs the following main functions:
• Prevention of condensation on both the inner and outer surfaces of the duct.
• Ensuring fire resistance to prevent the spread of fire in case of fire.
• Attenuation of noise and vibrations that occur during the movement of air through the duct.
• Reduction of heat transfer between the air flow in the duct and the environment.
For the organization of air ducts, materials with a zero (0) fire resistance class are used. If the channel has a multilayer lining, the fire resistance class "zero-one" (0–1) is allowed. This condition is met if all surfaces in the operating mode consist of non-combustible material with a thickness of at least 0.08 mm and if they provide continuous protection of the internal thermal insulation layer having a fire resistance class not higher than the first (1). Fasteners and connections whose length is not more than five times the diameter of the duct itself must be made of a material having a fire resistance class of "zero" (0), "zero-one" (0–1), "one-zero" (1–0), "one-one" (1–1) or "one" (1). Ducts of class "zero" (0) have an outer skin made of a material of fire resistance class not higher than the first (1).
Air treatment and air distribution systems create noise transmitted, among other things, through the duct system. It is possible to reduce noise if you maintain a low air velocity in the ducts, install damping devices at the point where the fan is connected to the duct, use an elastic suspension for the ducts, as well as damping gaskets at the points where the ducts intersect wall structures. The noise propagated through the air ducts can also be attenuated by the use of special silencers and a sound-proofing coating. Many thermal insulation materials have good sound insulation properties and can be used as both heat and sound insulation.
Thermal insulation of the duct can be performed from the inside or from the outside. When using thermal insulation inside the duct, it is necessary to increase the section of the duct to maintain the calculated carrying capacity at a given air velocity. In addition, the side of the thermal insulation in contact with the air flow should be smooth enough so as not to increase the resistance when air moves through the duct.
When installing silencers, the use of external thermal insulation is preferable. Also, the installation of external thermal insulation is the prevention of the occurrence of bacterial foci, the formation of dust and dirt deposits, due to which the thermal insulation material may begin to delaminate, release volatile substances and lose its qualities.
In addition, with external thermal insulation, the risk of fire spreading from room to room in the event of a fire is significantly reduced. The most important factor in the installation of thermal insulation is the prevention of thermal bridges that reduce the effectiveness of thermal insulation, as well as ensuring high vapor resistance. Heat transfer bridges can also occur in places where air ducts are attached to building structures.
The destruction of the thermal insulation material is prevented by:
• For internal thermal insulation – the use of composite materials, where thermal insulation is combined with a metal layer or film.
• For external thermal insulation – the use of neoprene sheathing, galvanized steel sheet or aluminum sheet.
Questions to Chapter 4
1. What are the disadvantages of circular ducts?
2. What are the advantages of rectangular ducts?
3. What material is used in the manufacture of air ducts for buildings and structures for general civil purposes?
4. What factors influence the choice of material for the manufacture of metal ducts?
5. How does the use of flexible air ducts affect the extended sections of the routes of ventilation systems?
Chapter V. Ventilation Parts and Network Equipment
5.1.Ventilation grilles
The grilles can be supply and exhaust. Those and others are adjustable and unregulated; round, square, rectangular; metal (more often steel or aluminum) or plastic; with and without decorative design; of various colors and sizes; with the direction of the flow of supply (or with the intake of the removed) air in one, two, three or four sides. Depending on the design of the grid, compact, flat, incomplete fan or other types of jets are created.
The control devices of the supply grids are the following types of regulators: flow regulator, jet characteristics regulator, direction regulator.
If the air distributor is equipped with more than one of the above regulators, then the regulating devices are usually installed in the same order along the air flow.
Exhaust grilles can also have flow and direction regulators. Some grid designs are universal and are used in both supply and exhaust systems.
Grilles are installed more often on the walls above the serviced area. At the same time, they can be specially designed for installation in the ceiling (for exhaust, inflow or universal).
5.2. Air distributors
The supply of the air in ducted and ductless air distribution systems is carried out in the form of jets.
Table 5.1 shows the schemes of air distribution devices and their main characteristics: aerodynamic coefficient m, temperature coefficient n and local resistance coefficient ξ. The coefficients m and n characterize the rate of attenuation of air velocity and temperature in the supply jet.Such indicators are necessary to calculate the speed and temperature of the air in the working area of the premises.
Table 5.1. Characteristics of air distribution devices
The choice of air supply methods depends on the height and purpose of the premises, the height and placement options of the equipment, as well as on the requirements for the uniformity of the distribution of air parameters.
Choosing the methods of air supply and removal, at the same time pre-select the supply and exhaust air distribution devices, their number and placement options relative to each other. The joint choice of air supply and removal methods is practically determined by the choice of the air distribution method in this room.
The applied methods of air distribution are characterized depending on the direction of movement of the air supplied to the premises: "from top to bottom", if the supply occurs in the upper zone, and removal – in the working; "from top to top", if the supply and removal of air occur in the upper zone of the premises, as a rule, this method ensures the movement of the supplied flows above the working level zones, and in the working area, the set air velocity is created by the reverse flow; "side up", etc. When choosing the method of air distribution, the direction of heat flows and the areas of the premises characterized by the maximum intake of heat or moisture are taken into account.
If it’s necessary to provide increased air velocity in air conditioning systems with an increased value of the height of the working area of the premises (hP. Z > 2 m) it’s possible to provide air distribution through conical nozzles.
The aerodynamic coefficient of conical nozzles m varies in a wide range, and its values depend on the angle of taper of the nozzle. Conical nozzles are characterized by the highest (maximum possible) values of the aerodynamic coefficient. As the taper angle increases, the value of m also increases. At the same time, the maximum value of m = 7.7 … 7.8. Simultaneously with an increase in m, the coefficient of local resistance also changes significantly. Figure 5.1 shows a diagram of a cylindrical nozzle with preload.
Supply grilles of various designs, ceiling lampshades and diffusers are also widely used, capable of working as supply and exhaust devices.
In rooms of small height (up to 5 m), air distribution can be carried out through perforated panels mounted in the ceiling. In this case, the normative mobility of air in the working area is achieved with a large multiplicity of air exchange. Perforation holes are made with a diameter of 2 to 10 mm, the area of the living section of the panel does not exceed 10% of the total area of the panel.
In air distributors-lamps, air is released (removed) through fluorescent lamps mounted in the suspended ceiling structure. Such a solution in the case of air extraction reduces the heat input from the lighting into the room, since part of this heat is carried away together with the exhaust air, moreover, due to the cooling of the lamps, it increases illumination.
A sufficiently satisfactory air distribution can be achieved by using perforated air ducts. The holes in the duct of variable cross-section length are located in its lower part.
Local exhaust ventilation is used when the places of harmful emissions in the room are localized and it is possible to prevent their spread throughout the room.
5.3. Devices for adjusting ventilation systems
General-purpose check valves are designed to prevent air from flowing through the branches to the disconnected fans (from the disconnected fans) when the latter are connected to the collectors. When installing valves in a vertical duct, the air flow should be directed from the bottom up. Installation of the valve in the network is allowed at air speeds in horizontal sections V ≥ 5…6m/s and on vertical V ≥ 4m/s.
The steel valve lobe valves in the usual design are designed to be installed on the discharge side of axial fans in order to prevent cold air and precipitation from entering the production premises after the fans are turned off. The design of the lobe valve is a housing in the bearings of which the blades are fixed on the axes. The purpose of the bearings is to ensure the free opening of the valve in conditions of negative external temperatures during periodic operation of the fans. When the fan is turned on, the blades are supported in the open position by the action of the airflow. After the fan is turned off, the blades return to their original position and overlap the valve section. In order to reduce the width of the valve, instead of switching from a circular fan section to a rectangular valve section, a transitional diaphragm is provided. The minimum dynamic pressure at which the lobe valve operates is 30…40 Pa.
Valves (dampers) air insulated designed for installation in low-pressure supply (exhaust) ventilation systems to prevent the penetration of outside air into the supply chambers and rooms when the fan is not working and to regulate the amount of air entering the system. The dampers can be either electrically heated or without it. The electric heaters in the valves serve only to warm up the flaps in case of icing, in order to prevent damage to the frozen flaps when opening. The electric heaters of the valves are switched on for 5–7 minutes before opening the valve. Valves (dampers) air insulated consist of a housing, double-walled rotary blades with thermal insulation properties, a drive and a motion transmission system from the drive to the blades. A rubber seal is installed at the interface points of the blades of the sound. An actuator is installed as a drive. It is possible to manufacture a manual-driven system. The maximum allowable pressure drop in the closed position is 1225 Pa (125 kgs/m2). Air passage in the closed position at a pressure drop of no more than 5%.
Resistance coefficient in the open position, not more than 0.2.
Dampers are available in the following types:
• Air unified;
• Round section with electric drive;
• Rectangular cross-section with electric drive;
• Circular cross section with manual drive;
• Rectangular cross-section with manual drive;
Air dampers are designed to regulate the amount of air and are used in air ventilation systems, air heating and other sanitary systems with an operating pressure of up to 1000 Pa.
Questions to Chapter 5
1. For what purpose are air distribution devices used?
2. Name the main characteristics of air distribution devices.
3. What factors are taken into account when choosing the type of air distribution device in the room?
4. What is the value of the dynamic pressure required for the operation of the lobe check valve?
5. What is the purpose of electric heating of air dampers, in which cases it is used?
Chapter VI. Mounting tools, fixtures and accessories for mechanization of installation work
Installation of ventilation systems is carried out by a team. As a rule, the integrated team of ventilation fitters includes two or three people with related specialties of an electric welder and a gas cutter. The numerical composition of the team is usually six to seven people. Each team is provided with a set of tools, which allows the team or its units to independently perform almost the entire scope of work on the installation of ventilation systems.
Table 6.1.
Table 6.2
Recommended set of electric welding equipment and tools for a team of locksmiths – ventilators
Table 6.3
Tools for gas cutting of steel
Table. 6.4.
Basic data of non-self-propelled inventory means of scaffolding and rigging
The connection of the end of the box with the flange is carried out using a TRUMPF TF 350–2 manual press. The fastening element is a "press rivet", which is cut and molded from the material of the workpiece in one working stroke of the punch (punch). This mechanical process of joining metal sheets is known as "offset connection" – the upper sheet is connected to the lower by kinematic closure. Its main advantage over traditional spot welding is that there is no damage to the surface due to heating, the butt joint is corrosion resistant. The TF 350–2 press is designed both for joining uncoated sheets and galvanized, painted, polymer-coated sheets. Preliminary and final processing with such "cold welding" is not required, there are no costs for screws, rivets and other connecting elements. For ease of operation, the punch, which forms the "rivet" with a continuous pressing blow, is installed in a movable lever. Thus, the tool frame can be "opened" with a single movement of the hand in order to easily and quickly install the tool at the desired point of the tire. At the same time, the flange height is allowed up to 40mm. A special cone puller makes it possible to fasten the tire with the box as close as possible to the edge of the duct. Depending on the technical and aesthetic requirements, the connecting element can be concave into the surface of the box or protrude above the surface. It is possible to obtain an almost airtight connection for sheets of various thicknesses by choosing the appropriate matrix size. A set of tools is installed on the TRUMPF TF 350–2 press, in accordance with the specified total thickness of the sheets. Tool change is quick and easy and does not require special tools or skills. The productivity of the TRUMPF TF 350–2 press is 2 rivets per second. The tool is suitable for both portable and stationary applications.
Seam connection. The Pittsburgh fold is an ideal connection method for straight or curved boxes. A smooth, dense and aesthetic connection is obtained without any additional processing when using TRUMPF F 300 series tools. The Pittsburgh fold ("American") is obtained by continuous roller running-in, without damaging the surface and coating. Automatic feed control guarantees seam accuracy and uniform joint density. TRUMPF folding machines are suitable for both straight boxes and bends, with a minimum internal radius of only 300 mm.
To install grilles, blinds, valves and air conditioners themselves, it is often necessary to make cutouts in an already mounted box. Especially for this application, TRUMPF has developed the C 160 slotted scissors, which allow you to make cutouts with great accuracy, without deforming the sheet, and the chips do not get inside the box, because they stand out above the surface of the sheet with a continuous tape. You can start and finish the cut at any point on the surface of the box; by turning the small handle on the cutting head, the chips are bitten off at the desired point. The edge of the cut is perfectly smooth. These scissors can be used to cut welded spiral seams on round ducts up to 2.5 mm thick.
Questions to Chapter 6
1. Name the composition of the joint team of locksmiths.
2. Explain the principle of operation of the instrument from the main set (one, at the student's choice).
3. Describe the method of connecting the flange to the end of the duct.
4. What is the reason for the location of the connecting element relative to the duct?
5. What are the advantages of a folding connection?
Chapter VII. Installation of ventilation equipment
The production of installation ventilation works at facilities implies preparation for the installation of ventilation equipment, which requires careful preparatory work. Special attention should be paid to the reality of the implementation of design solutions by the installation team, both technically and in terms of execution.
7.1.Projects of production of works
The project of work production is the basic guide for the organization and production of installation work at the facility. Project of work production helps to plan all the preparatory work, including the execution of orders for air ducts and applications for ventilation equipment and materials, to determine the storage locations of bulky ventilation parts. The project of work production contributes to the uninterrupted conduct of installation work, improving the quality of installation.
The complete project of work includes the following sections:
1) situational master plan, usually on a scale of 1:400, with reference to the storage locations of air ducts and ventilation equipment and an intra-building transport scheme;
2) schematic plan of the object with drawing of axes and locations of ventilation equipment;
3) list of ventilation equipment supplied by the customer;
4) characteristics of air ducts for ventilation systems and a list of installation drawings or sketches on them;
5) schedule of receipt of ventilation blanks (ducts and standard ventilation parts) to the facility;
6) the schedule of receipt of ventilation equipment, agreed with the customer;
7) calendar (network) schedule of work with deadlines for the delivery of the object;
8) statement of basic and auxiliary materials;
9) instructions on methods and methods of installation work and safety;
10) a statement of the necessary mechanisms, tools and means of small mechanization specifically for the object;
11) production calculations and summary statements of labor costs and wages;
12) the schedule of the need for workers.
In the calendar (network) schedule of work, the deadlines for preparing the object or individual premises for installation, the deadlines for the completion of construction work in ventilation chambers, the deadlines for the supply of electricity to ventilation equipment and hot water to heaters and, most importantly, the deadlines for the installation of ventilation systems should be determined. A schedule for the delivery of ventilation equipment to the facility must be agreed with the customer's organization in advance.
For objects with a small amount of ventilation work and capital repairs, abbreviated The project of work production is the basic guide for the organization and production of installation work at the facility. Project of work production helps to plan all the preparatory work, including the execution of orders for air ducts and applications for ventilation equipment and materials, to determine the storage locations of bulky ventilation parts. The project of work production contributes to the uninterrupted conduct of installation work, improving the quality of installation.
7.2. Acceptance of the object for installation work
Prior to the start of installation work on the object or on its part, a list of individual types of construction works, the performance of which is necessary for the subsequent installation of ventilation systems, and the timing of their execution must be agreed between the representatives of the installation organization and the general contractor.
Such works include:
1) installation of foundations, platforms and other supporting structures for ventilation equipment;
2) installation of walls and partitions in ventilation chambers, as well as ceilings, if the project of work production does not provide for the supply of ventilation equipment through the top of the chambers;
3) installation of embedded parts provided for by the project in ventilation chambers for connecting ventilation equipment and along the route of systems for fixing air ducts;
4) installation of horizontal and vertical mounting openings for the supply of ventilation equipment and ducts from an on-site warehouse to the place of their installation;
5) installation of walls and ceilings in the places of laying air ducts;
6) plastering and painting of walls, ceilings and partitions in the places of laying air ducts and installing air distributors;
7) punching holes in places where air ducts pass through walls, ceilings and partitions, if they are not left during the construction of the building;
8) installation of reinforced concrete cups on floors in places of passage of ventilation shafts and installation of roof fans;
9) the device of fasteners for large-sized air ducts and platforms for cyclones, scrubbers, filters, etc.;
10) the device of ventilation ducts in construction (brick, concrete);
11) glazing of window openings and lanterns
12) cleaning of ventilation work sites from construction debris.
After performing these works on the entire object, the object is accepted under a bilateral act for installation. It is especially necessary to carefully prepare the rooms of the ventilation chambers, where all construction work (except clean floors and final painting) must be carried out and the lifting devices provided for by the project for the operation and repair of ventilation equipment must be installed. For the passage of air ducts through building structures, the holes in them must be 150 mm larger than the diameter of a round or the dimensions of the sides of a rectangular air duct.
By the time the installation works begin, the general contractor must provide the installation team with:
a) cabins for workers, a room for a workshop and a storeroom, open storage areas and sheds for storing air ducts, ventilation equipment and products in the area of operation of vehicles;
b) supply of electricity, water and heat during the cold period for the production of works and for domestic premises;
c) vertical and horizontal on-site transport;
d) electric lighting in places where ventilation works are performed;
e) fire and guard protection.
To perform installation work directly on the site, it is necessary to have the following technical documentation:
1) two copies of working drawings;
2) a set of installation drawings or sketches for all ventilation systems;
3) a project for the production of works with standard technological maps;
4) the list of ventilation equipment and materials supplied by the customer (non-standard equipment, alloy steel, etc.);
5) the act of acceptance of the object for installation.
After acceptance of the object for installation, mounting devices (ladders, towers, traverses, blocks, scaffolds, etc.), mounting mechanisms, electrified tools, welding equipment and tool kits are delivered to the object.
7.3. Installation design
Air ducts of ventilation systems are manufactured only according to installation drawings or sketches. Installation drawings are carried out on the basis of working drawings of ventilation systems.
Installation drawings contain:
a) an axonometric diagram of each ventilation system, made without a scale in one line, indicating the dimensions of the cross-sections of the ducts, the number of each part, marks and bindings of the ducts to the axes and surfaces of building structures;
b) a complete list with a list of all parts, their dimensions, characteristics, quantity;
c) sketches of non-normalized shaped parts of air ducts with all the dimensions required for their manufacture;
d) the scope of work and specification of materials and standard components, including the type and number of fasteners.
7.4. Installation of fans
Installation of fans up to and including No. 12 is carried out in the following sequence:
1) check the prefabricated structures on which the fan should be mounted;